Producing an aluminum pergola is a multifaceted process that involves several stages, from initial design to final installation. Each stage requires careful planning, precision, and attention to detail to ensure the pergola meets the desired specifications and quality standards. Here’s a comprehensive breakdown of the production process:
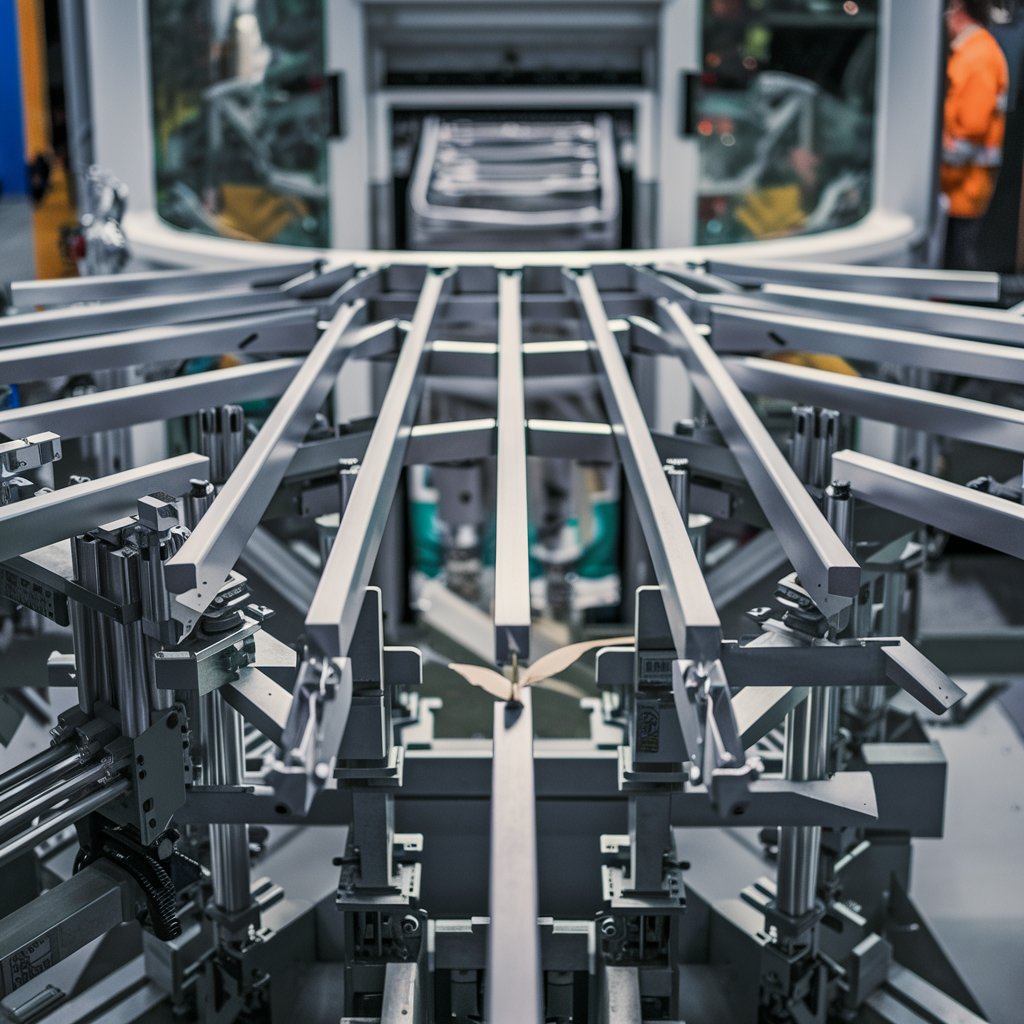
1. Design and Planning
Conceptual Design
The journey begins with the conceptual design phase, where the vision for the pergola is brought to life. During this phase, the requirements and specifications are determined, including the dimensions, style, and any additional features. This phase often involves collaboration between the client, architects, and engineers to ensure the design meets both aesthetic and functional needs.
- Client Requirements: Understanding the client’s needs and preferences is crucial. This includes the intended use of the pergola, whether for residential or commercial purposes, the desired look, and any specific features such as lighting, retractable canopies, or integrated heating systems.
- Site Analysis: Analyzing the installation site helps in understanding the environmental conditions, space constraints, and any potential challenges. Factors like wind load, sun exposure, and local building codes are considered during this analysis.
Engineering and CAD Drawings
Once the conceptual design is approved, detailed engineering and CAD (Computer-Aided Design) drawings are created. These drawings provide precise specifications and dimensions for every component of the pergola.
- Structural Analysis: Engineers conduct structural analysis to ensure the pergola can withstand various loads and stresses. This includes calculations for wind load, snow load, and any additional weights the structure might bear.
- Component Specifications: Detailed drawings specify the dimensions, shapes, and materials of all components, such as beams, posts, rafters, and connectors. This ensures that each part is manufactured to exact standards.
- Integration of Features: If the pergola includes additional features like lighting or a retractable canopy, these elements are integrated into the CAD drawings to ensure a seamless final product.
2. Material Selection
Aluminum Alloys
Selecting the right aluminum alloy is critical for the pergola’s strength, durability, and resistance to corrosion. Commonly used alloys include 6061 and 6063, known for their excellent mechanical properties and suitability for extrusion.
- 6061 Alloy: Known for its good mechanical properties and weldability, 6061 aluminum is often used in structural applications. It provides a good balance of strength, corrosion resistance, and ease of fabrication.
- 6063 Alloy: This alloy is known for its excellent extrudability and is often used for architectural applications. It provides a high-quality surface finish and is ideal for creating intricate shapes.
Surface Finish
The surface finish of the aluminum components plays a crucial role in the pergola’s appearance and durability. Common finishes include anodizing and powder coating.
- Anodizing: This electrochemical process enhances the natural oxide layer on the aluminum surface, improving corrosion resistance and allowing for a range of color options.
- Powder Coating: Involves applying a dry powder to the aluminum surface, which is then cured under heat to form a protective layer. Powder coating provides a durable, high-quality finish and is available in a wide range of colors and textures.
3. Extrusion
Extrusion Process
The extrusion process transforms aluminum billets into the specific shapes and profiles required for the pergola components.
- Heating and Forcing: Aluminum billets are heated to a specific temperature, making them malleable. The heated billets are then forced through a die, which shapes the aluminum into the desired profile.
- Precision Profiles: The extrusion process allows for precise control over the shape and dimensions of the aluminum profiles, ensuring they meet the design specifications.
Cooling and Cutting
Once the aluminum profiles are extruded, they undergo cooling and cutting.
- Cooling: The extruded aluminum profiles are cooled using air or water to solidify their shape.
- Cutting to Length: After cooling, the profiles are cut to the required lengths specified in the design. This step ensures that each component is ready for further fabrication.
4. Fabrication
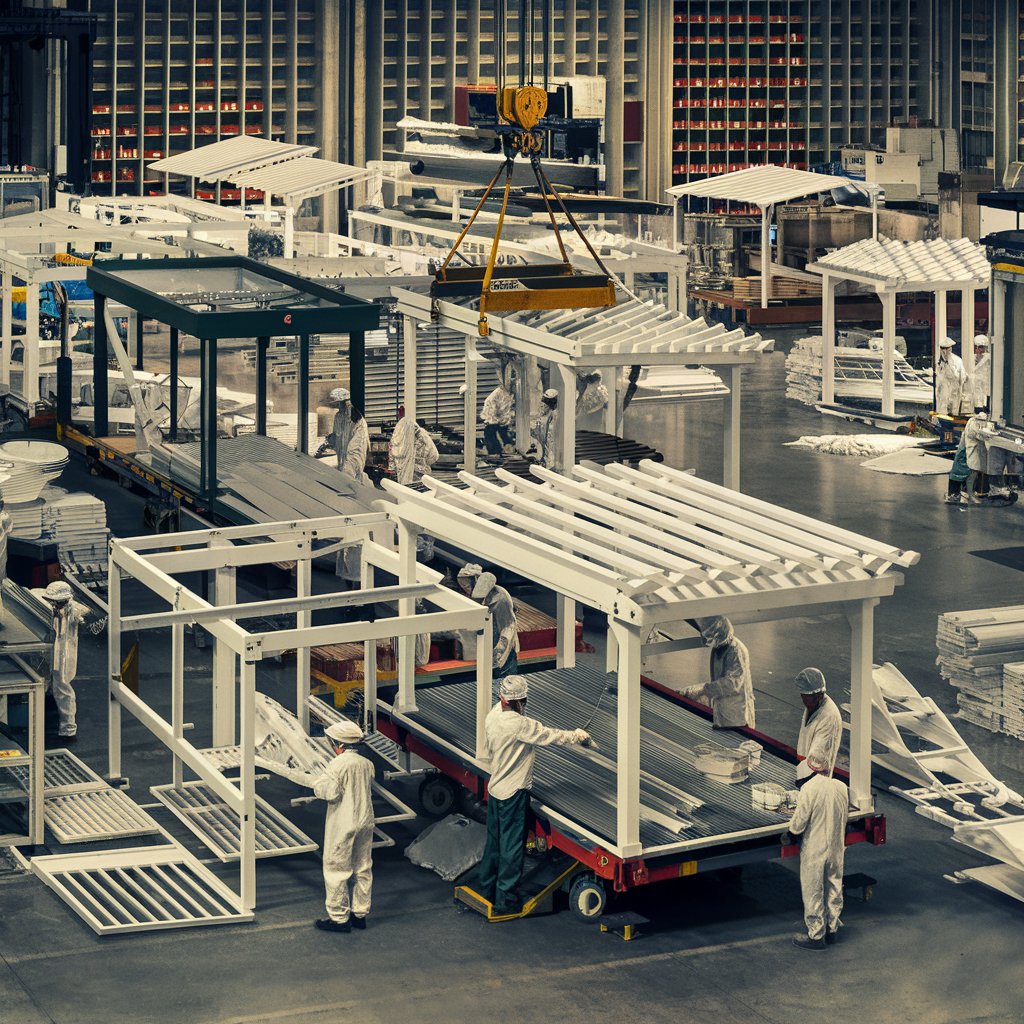
Cutting and Machining
The extruded profiles undergo further cutting and machining to fit the design specifications.
- Precision Cutting: The aluminum profiles are cut to exact lengths and angles using precision cutting tools. This ensures that all components fit together correctly during assembly.
- Drilling and Machining: Holes are drilled, and additional machining is performed to create joints and connections. This includes making holes for fasteners, creating slots for brackets, and any other necessary modifications.
Welding and Assembly
Some parts may require welding and assembly to form larger components or complex shapes.
- Welding: Welding is used to join aluminum parts that cannot be connected using fasteners. This is common for custom or complex designs where a seamless connection is required.
- Sub-Assembly: Components are pre-assembled into sub-assemblies where feasible. This helps streamline the final installation process and ensures that parts fit together correctly.
5. Surface Treatment
Cleaning and Pre-treatment
Before applying the final surface finish, the aluminum parts undergo cleaning and pre-treatment to ensure the coating adheres properly.
- Degreasing and Cleaning: The parts are cleaned to remove any oils, grease, or contaminants from the surface. This is typically done using chemical cleaners or ultrasonic cleaning methods.
- Etching and Rinsing: The aluminum is etched to create a uniform surface texture, followed by rinsing to remove any residues. This step enhances the adhesion of the surface finish.
Anodizing or Powder Coating
The cleaned and pre-treated parts are then subjected to the chosen surface treatment.
- Anodizing: Anodizing involves immersing the aluminum parts in an electrolytic solution and applying an electric current. This process thickens the natural oxide layer, improving corrosion resistance and allowing for various color options.
- Powder Coating: In powder coating, a dry powder is electrostatically applied to the aluminum surface. The coated parts are then cured in an oven, creating a hard, durable finish that resists chipping, scratching, and fading.
6. Quality Control
Inspection
Quality control is essential to ensure that each component meets the design specifications and quality standards.
- Dimensional Inspection: Each component is measured to verify that it meets the specified dimensions and tolerances. This includes checking lengths, angles, and hole placements.
- Surface Finish Inspection: The surface finish is inspected for uniformity, adhesion, and any defects such as scratches or blemishes.
Testing
In addition to visual and dimensional inspections, structural tests may be performed to ensure the components meet safety and load-bearing requirements.
- Load Testing: Structural components may be subjected to load tests to verify their strength and stability. This ensures that the pergola can safely support the intended loads, including wind, snow, and any additional weights.
- Corrosion Resistance Testing: Parts may be tested for corrosion resistance, especially if the pergola will be installed in a harsh environment. This ensures that the surface treatment provides adequate protection against corrosion.
7. Packaging and Shipping
Packaging
The finished components are carefully packaged to prevent damage during transportation.
- Protective Packaging: Each part is wrapped or covered with protective materials, such as bubble wrap, foam, or corrugated cardboard, to prevent scratches and dents.
- Organized Packing: Components are organized and labeled to facilitate easy assembly at the installation site. This includes grouping related parts and providing clear instructions.
Shipping
The packaged components are shipped to the installation site or the end customer.
- Logistics Planning: Efficient logistics planning ensures that the components arrive at the installation site on time and in good condition. This includes selecting reliable shipping partners and coordinating delivery schedules.
- Handling and Transportation: Proper handling and transportation methods are used to prevent damage during transit. This includes using appropriate vehicles and securing the packages to prevent shifting.
8. Installation
Site Preparation
The installation site is prepared to ensure a smooth and successful installation process.
- Ground Preparation: The ground is leveled, and any necessary foundations are set. This may involve pouring concrete footings or installing anchor systems to provide a stable base for the pergola.
- Layout and Marking: The layout of the pergola is marked on the ground to guide the installation process. This includes marking the positions of posts, beams, and other components.
Assembly
The aluminum pergola components are assembled on-site according to the design plans.
- Erecting Posts: The posts are installed first, providing the vertical support for the pergola. They are securely anchored to the ground or foundation to ensure stability.
- Attaching Beams and Rafters: Beams are attached to the posts, followed by the rafters. The components are secured using fasteners and brackets, ensuring that all connections are tight and aligned.
- Integrating Additional Features: If the pergola includes additional features like lighting, a retractable canopy, or heating systems, these elements are integrated during the assembly process.
Final Inspection
A final inspection is conducted to ensure the pergola is properly installed and meets all safety and design standards.
- Structural Inspection: The structure is inspected to verify that all connections are secure and that the pergola is stable and level.
- Functional Testing: Any additional features, such as lighting or retractable canopies, are tested to ensure they function correctly.
- Aesthetic Inspection: The final appearance of the pergola is inspected to ensure it meets the client’s expectations and the design specifications.
Conclusion
The production process of an aluminum pergola is a complex and detailed endeavor, requiring careful planning, precision engineering, and high-quality materials. From the initial design and material selection to the final installation, each step is crucial to creating a durable, aesthetically pleasing, and functional pergola. By following these detailed stages, manufacturers can ensure that their aluminum pergolas meet the highest standards of quality and performance, providing customers with a beautiful and long-lasting outdoor structure.
4o